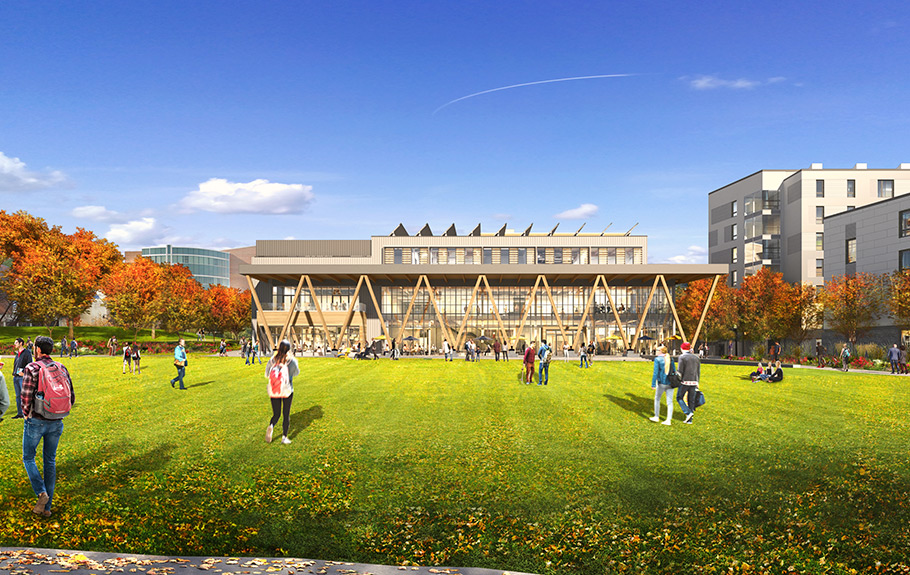
Or, if you would rather have someone show you around, please visit our contact page to schedule an in-person tour with one of our McGoldrick green building tour guides.
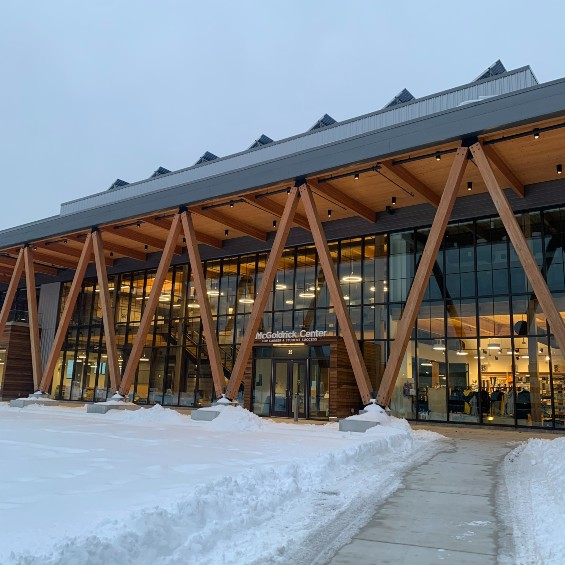
One of the intentions of LEED certification is to have a LEED AP quarterbacking the coordination of sustainability features of a building’s design and construction. In addition, the goal is to have the owner, the developer, the architects, the engineers, the general contractor, and the sub contractors all talking to each other on a regular basis and communicating about important decisions in design and implementation. In the fast-paced building industry, it is easy to skimp on this communication without a program like LEED necessitating tight coordination.
If you don’t establish energy goals to meet and don’t talk to the mechanical and electrical contractors about those goals, then a building is likely not going to be energy efficient. Similarly, if you don’t establish goals for recycled, local, or low VOC materials and communicate them to the architects and engineers, then you can’t expect your building to contain healthy air and reflect your values as an institution. The average academic building or residence hall at a University requires over 100 individuals to source, design, and construct. There are infinite possibilities for miscommunication without having a well defined process for sharing ideas, making decisions, and coordinating activities.
During the design and construction phases of the McGoldrick Center, our LEED consultant, the University’s director of sustainability, and point people from all the major contractors met regularly to coordinate, share ideas, and challenge each other to build the best building they could.
Green buildings are not always built on green sites. When a green building can be sited carefully and mindfully on soil that has sustained a history of industrial use, it can be a great use of space that might otherwise not be a good candidate for agricultural use or habitat rehabilitation. Siting buildings in areas like this may be preferable to clear cutting forest or other natural environments.
The McGoldrick Center was sited on land that was predominately comprised of urban fill. A parking lot, tractor company and orchard had all utilized the land in the past, creating less than ideal soil conditions. In the planning for the McGoldrick Center, the University worked with an environmental company to create a soil management plan to keep the site safe for current and future generations and also entered the Department of Environmental Protection’s Voluntary Response Action Program (VRAP) as a proactive measure for responsible stewardship.
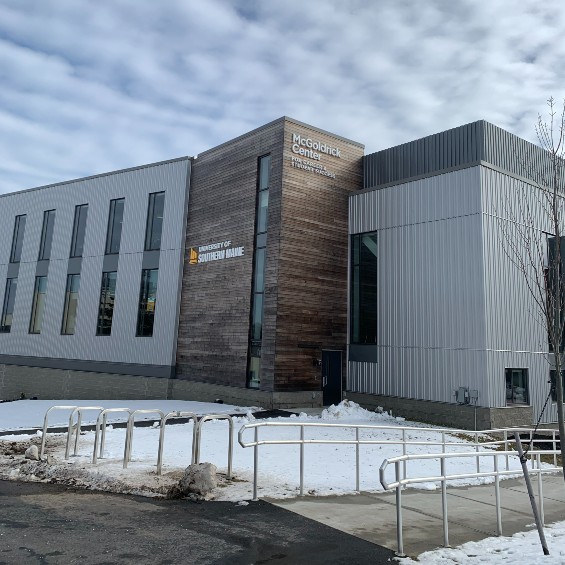
Density and diversity are critical ingredients to creating built environments where residents can easily ditch their single occupancy vehicles and take off on foot, grab a bicycle or hop on the bus. Density is important in order to create the critical mass of people necessary to make public transportation, such as buses and trains, viable. Density is also important in incentivizing businesses to set up shop close to residential areas. The McGoldrick Center was built in one of the denser neighborhoods in the State of Maine.
Diversity is useful for creating sustainable transportation-conducive environments because it ensures that people can easily get their basic needs met in close proximity to where they live. The McGoldrick Center was built within half of a mile of a range of different businesses and services including a grocery store, restaurants such as fast food establishments and pizza places, exercise venues such as gyms and public parks, a bank, a pharmacy, and two medical clinics.
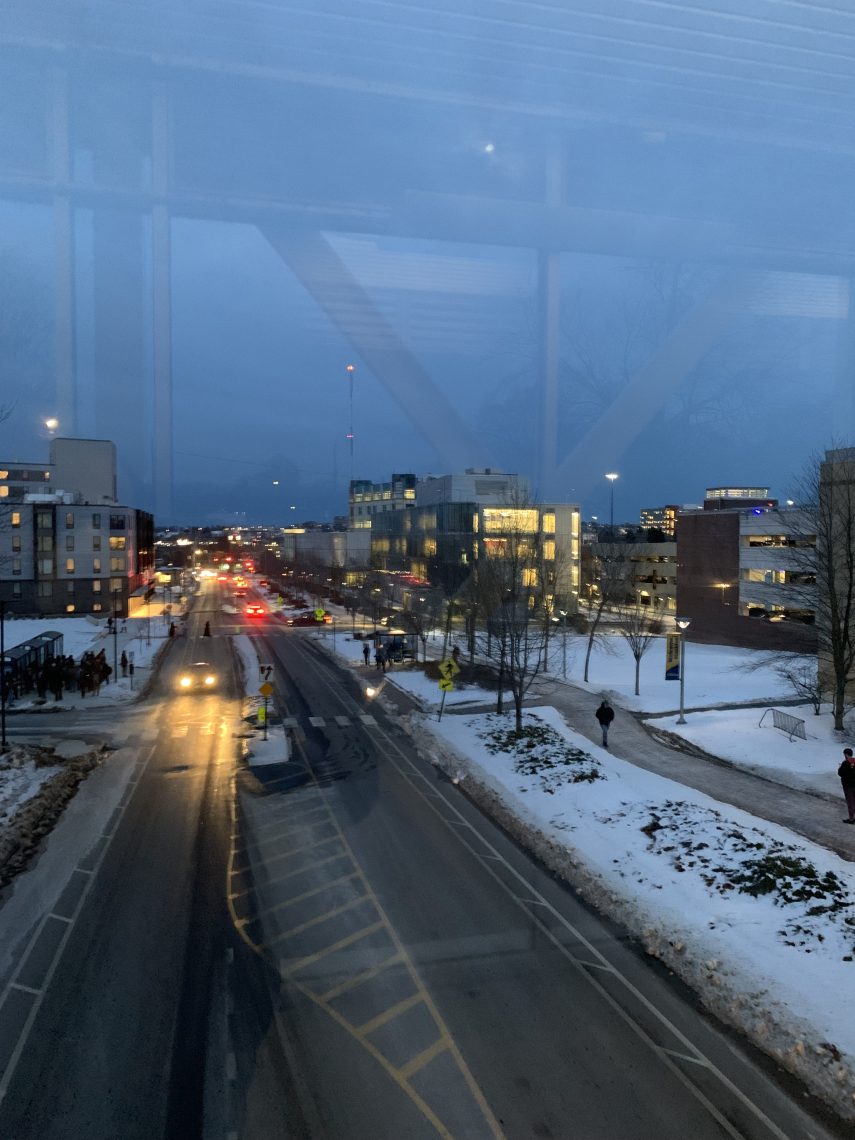
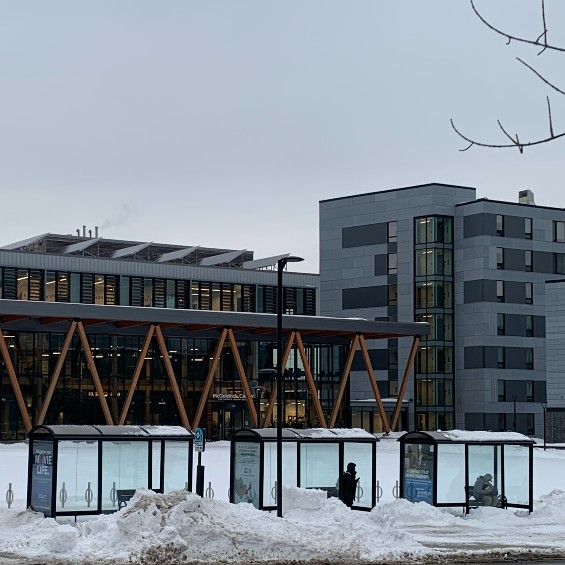
The McGoldrick Center is approximately 30 yards away from two major bus stops served by the Greater Portland METRO. The bus shelters shown above comprise the outbound bus stop for the Husky Line. The Husky Line provides frequent bus service to and from USM’s Gorham campus, with stops along the way in the City of Westbrook. Students, staff, faculty and visitors who want to travel to downtown Portland can easily hop on the inbound Husky Line. Additional bus routes passing campus include METRO’s route 4 and route 2, as well as the Zoom Express 70, the RTP Lakes Region’s Explorer, and others.
University students, staff and faculty can ride the Greater Portland METRO for free by simply tapping their University Husky card. Because of how easy it is to hop on a bus and ride from the heart of campus, recent transportation surveys show that between 25-30% of the miles traveled to campus among University affiliates are by non-single occupancy vehicles.
For more information about the University of Southern Maine’s bus services, please visit this page.
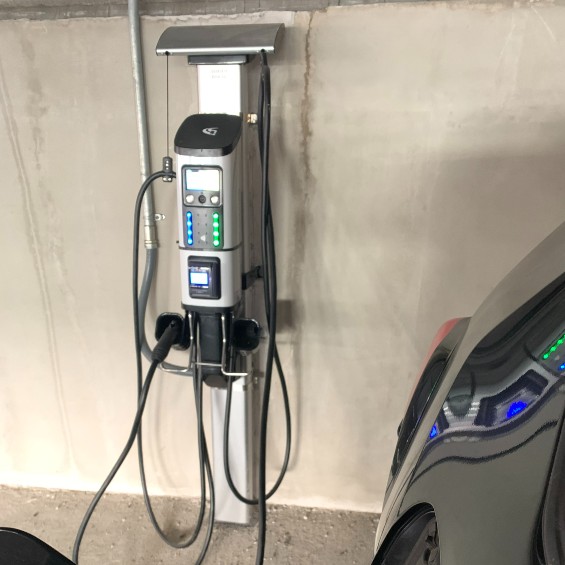
At the time the McGoldrick Center was built, the University installed 58 level-2 EV vehicle charging plugs in the parking garage across the street from the building. They are less than 400 feet from the front entrance to McGoldrick and are available for use by students, staff, faculty or visitors with a valid permit. At the time of installation, this was the largest collection of level-2 charging stations in Maine. Each charging plug was put on a dedicated circuit, allowing for the maximum charge rate allowed by the device, regardless of how many other vehicles are charging in the area.
The charging stations are from SemaConnect, which is now owned by Blink. For more information about charging prices and policy, please visit the EV page here.
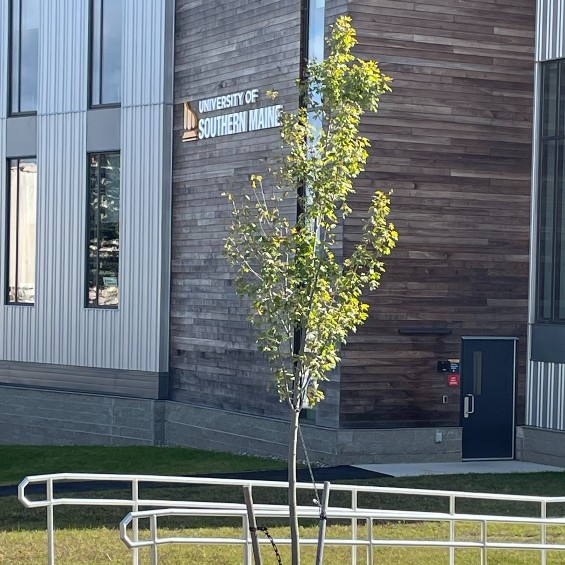
A majority of the flora planted outside of the McGoldrick Center are native or native hybrids (the tree featured above is an Acer x freemani, which is a cross between the native red and silver maples). Native plants and trees provide more food and more appropriate habitat for native insects and native birds than non-native varieties. They are also more appropriate for the local climate. This tolerance for the local climate makes them more better equipped for handling the local weather, including the level of moisture and the temperature that is typical for the area. Less pesticides and less irrigation are needed as a result. The native sedges shown below include Carex pennsylvanica and Carex stricta.
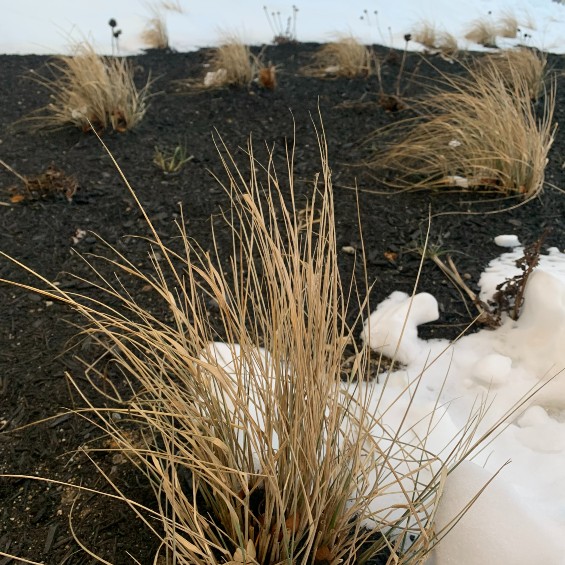
In instances where non-native flora were planted around McGoldrick, they were at least chosen to be climate appropriate.
The trees planted around McGoldrick include:
- Amelanchier x grandiflora ‘Autumn Brilliance’
- Acer x freemani ‘Armstrong’
- Betula nigra ‘Heritage’
- Malus ‘Adirondack’
- Tilia cordata ‘Greenspire’
- Zelkova serrata ‘Musashino’
The shrubs include:
- Arctostaphylos uva-ursi
- Azalea ‘Karen’
- Juniperus horzontalis ‘Bar Harbor’
- Rhododendron laetivirens ‘Wilson’
- Stewartia pseudocamellia
- Thuja occidentalis ‘Nigra’
The plants include:
- Calamagrostis x accutifolia ‘Karl Foerster’
- Carex pennsylvanica
- Carex stricta
- Dennstaedtia punctiloba
- Eutrochium purpureum
- Echinacea Sombrero Lemon Yellow
- Festuca ovina glauca
- Hosta ‘Dream Weaver’
- Nepeta ‘Early Bird’
- Osmunda cinnamomea
- Sughastrum nutens
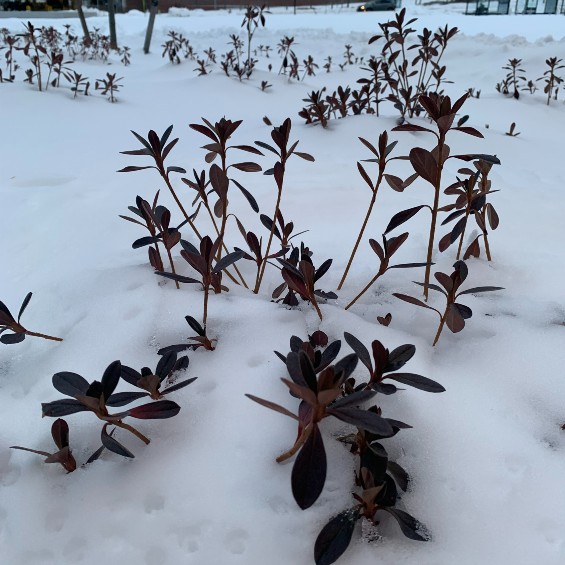
Having sufficient space is an important green building characteristic because it is conducive to mental health and provides ecosystem benefits. Over 65% of the McGoldrick Center’s project site is open space.
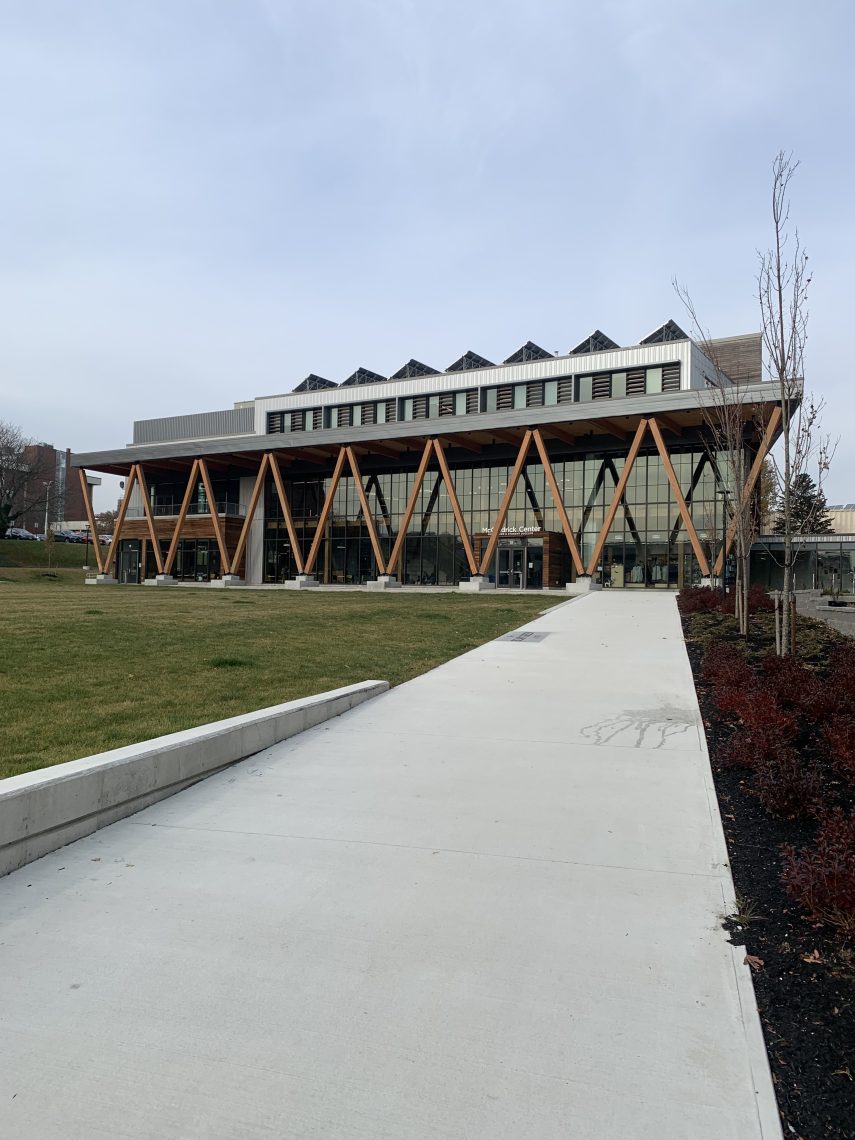
All of the paving around the McGoldrick Center is pedestrian-oriented with associated landscaping that is accessible to all and meant to encourage walking on campus. Students, staff and faculty can hang out on the green spaces around McGoldrick to socialize and collaborate. Around the large quad there are concrete steps to provide space and seating for people to congregate and socialize, while accessing the quad lawn for use for events and playing.
LEED projects promote vegetated space that is not just turf grass. The McGoldrick Center’s non turf grass space comprises almost 33% of the open area. For example, near the edge of the campus there are landscape areas and diverse plantings to provide a relaxing and interesting environment near the bus stops. Trees along the edges of the quad provide shade and allow for comfortable walking experience from the street to the McGoldrick Center and onward to the rest of campus. On the north side of the building, a beautiful rain garden area has been planted with a wetland herbaceous plants, as well as woody evergreens. A row of large trees that were preserved by the project also line the edge of a second green that includes a public art display and open space for recreation.
Rainwater management is the process of collecting stormwater and controlling it in a mindful way so that it minimizes pollution into nearby water bodies. Surface pollutants like residual oils and chemicals can be harmful to aquatic ecosystems if they enter streams, rivers, lakes, ponds, and the ocean.
For the McGoldrick Center, the team installed an underdrained soil filter in accordance with Maine Chapter 500 stormwater regulations. Soil filters are designed to remove pollutants and channel protection as they provide the slow release of runoff. The filter also provides cooling of the discharge, reducing thermal impacts to downstream water bodies.
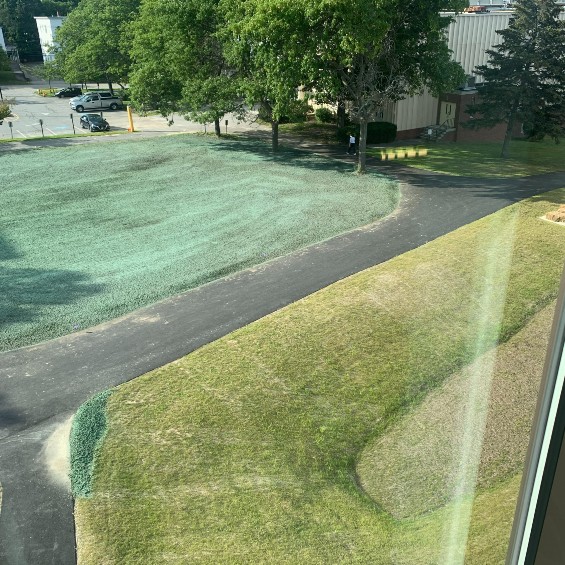
The University made sure that the stormwater system could handle the heavy rainstorms that are expected to become more normal as climate change intensifies. In general, the University takes stormwater very seriously, and has comprehensive stormwater management plans for its campuses. You can learn more about our stormwater plans here.
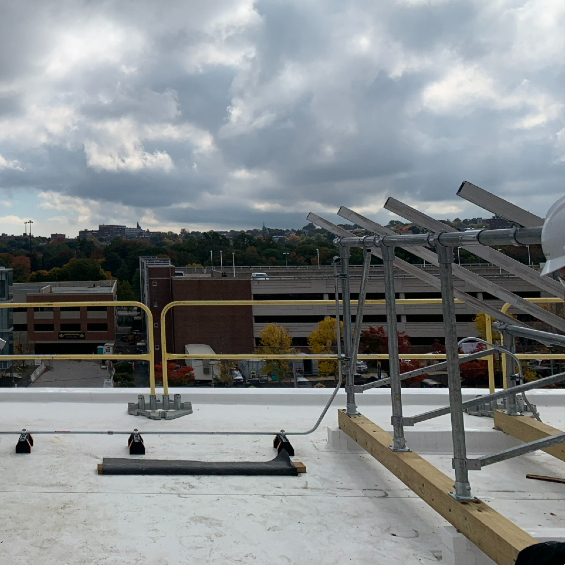
Urban environments, like the Portland campus, can heat up in warmer weather more than the surrounding environment. This is because of a phenomenon called the “heat island effect.” This phenomenon occurs when dark surfaces like pavement and the roofs of buildings absorb lots of short wave radiation from the sun and hold onto that heat locally. The result is that urban neighborhoods can actually feel warmer than suburban or rural neighborhoods. When this occurs in the summer during a hot spell, it can be detrimental to human health for those who are spending time outdoors.
To reduce this heat island effect, the McGoldrick center has a special roof top made of white TPO. In simple terms, this white top has high albedo, meaning it has high reflectivity for solar radiation. When short wave radiation beams down from the sun, the white surface reflects more of that radiation directly back into the atmosphere than it would if it was a darker color. This strategy can help reduce the local heat island effect during some of the hottest days of the year. In technical terms, the three-year aged SRI or Solar Reflect Index value of the McGoldrick Center’s roof material is 85, exceeding LEED specifications that it be at least 64.
The hard surfaces around the McGoldrick Center were also mindfully designed in order to maximize albedo. The white cement concrete used on the site has a three-year aged SRI of .35, exceeding LEED specifications that it be at least .28.
Additionally, the trees and plants installed for the landscaping around the McGoldrick Center are anticipated to provide a canopy of 3,620 feet within 10 years, which will provide additional protection against the heat island effect.
In a place like Maine, people may wonder why it’s important to save water. They may think that’s just something that southwestern states have to worry about. LEED offers points for water conservation wherever you are because the use of potable water impacts the environment even in wet climates. First of all, most potable water in the US is not potable straight out of the lakes or rivers it comes from without first being treated. The process of treating that water requires massive resources, such as energy, chemicals and materials. All of these inputs have environmental impacts. Then, after the water is used, it needs to be treated again in different ways before it re-enters the environment. Therefore, the less water we use, the more inputs we can conserve, and the lower the environmental footprint will be.
In addition to the impact of treating water, there is also an impact for heating water. Warm water is available in the kitchen and bathroom sinks in the McGoldrick Center, like it is in most modern buildings. Warming that water requires a heating system that uses some kind of fuel. In the case of the McGoldrick Center, that fuel is natural gas. Therefore, using less water results in using less fossil fuels.
To save water in buildings like McGoldrick, the typical strategy is to restrict the flow of water coming out of fixtures and/or to add air to it to make it “fluffier.” When it comes to toilets, the primary strategy is to make sure that the toilets are designed to use less water with every flush. We refer to fixtures and toilets like this as “water efficient”. The bathroom faucet below is considered “water efficient” because it only allows for the flow of .35 gpm (gallons per minute) of water, which is less than the LEED standard of .5 gpm. This faucet also has an aerator in it to make the water “fluffier” by spreading it out, so that it is more effective at washing peoples’ hands even though it’s using less.
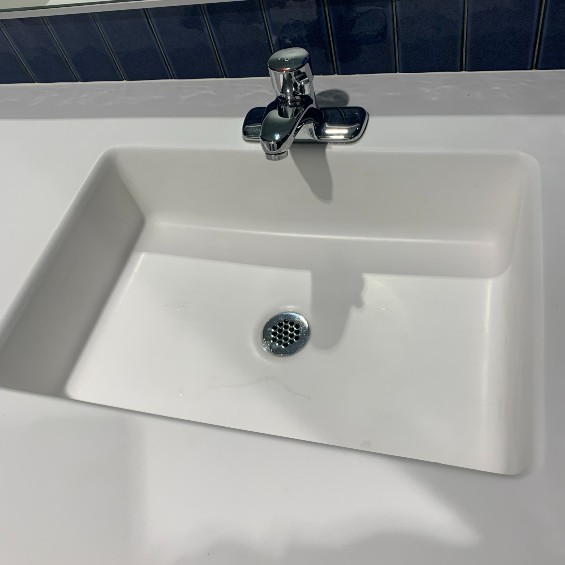
Other water efficient fixtures in the building include automatic flush toilets that only use 1.1 to 1.6 (gpf) gallons per flush, manual flush toiles that only use 1.28 (gpf) gallons per flush, automatic urinals that only use between .125- 1 gpf (depending on the settings), and various kitchen sink faucets that only use 1 gpm, 1.15, 1.5 gpm and 2.2 gpm, respectively. The 2.2 gpm model includes an aerator to help maximize the utility of the water. All of these meet or exceed LEED’s water efficiency standards.
Additionally, the building contains water-using appliances that are either Energy-star, ISO-certified to be water efficient, or the equivalent, such as the dishwashers in the kitchen or the ice maker.
All of the water saving methods employed above are projected to reduce baseline water use by 33.7% compared to what the use would have been otherwise.
Commissioning is the important process of making sure that all of a building’s heating, cooling, and ventilation systems are designed appropriately, installed correctly, functioning adequately, and that the building’s owners are thoroughly trained on how they operate. It may seem like common sense to go through this type of process, but unless an explicit structure is put in place to ensure it gets done, it may not get done.
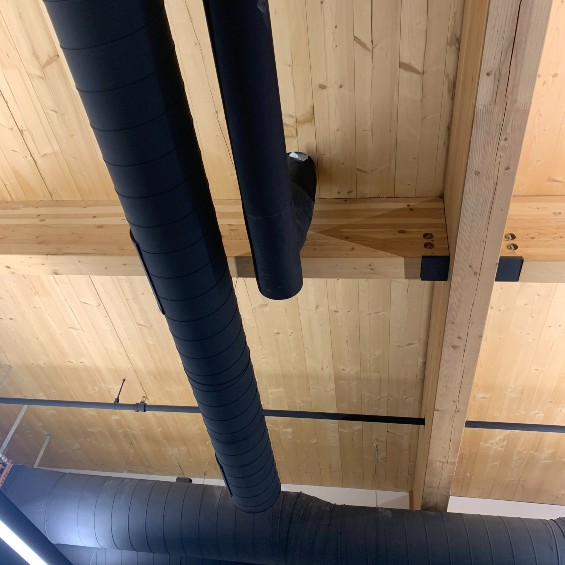
The McGoldrick Center earned LEED points for enhanced commissioning with the help of Steven Winter Associates. Steven Winter Associates reviewed plans, tested the systems, trained University of Southern Maine staff on the building’s systems, drafted manuals, and set up an operations and maintenance plan. Training not only includes how the mechanical and electrical systems work, but also what error codes and warning sounds mean. Such knowledge pays dividends down the road when the University’s maintenance team can identify problems early on and act to adjust settings or replace parts, which can save fuel, electricity and carbon emissions. In addition to covering the normal heating, cooling and ventilation systems, the commissioning also covered other large mechanical equipment, such as the window shades, the trash and recycling compactors, electric metering, elevators, sump pumps, plumbing, water heaters, lighting control devices, and the fire alarm system.
In addition to ensuring proper operation of all these items in the commissioning process, Steve Winter Associates also covered safety precautions and protocols. A smart building is not just one that saves energy and keeps occupants comfortable, it is also one that prevents fire, electrocution and water leaks.
The McGoldrick Center is built to be more efficient than your average building built to code. Energy Star appliances throughout the building, energy-efficient lights, occupancy sensors and highly efficient boilers, water heaters, and chilling equipment all contribute to this outcome.
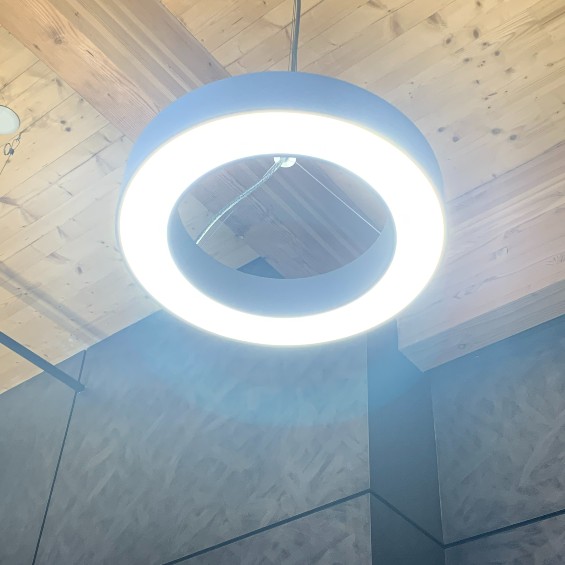
One of the most common ways of comparing the energy efficiency of different buildings is by examining how much energy each building uses annually per square foot. The energy use includes fuels and/or electricity used to heat, cool, and electrify the building. We call this EUI or Energy Use Intensity. To do this calculation, we need to convert all energy forms into one unit. The most commonly used is a Btu or British Thermal Unit. Because Btus are small, we often count them in thousands, which is denoted by a k in front of the Btu. The McGoldrick Center is designed to have a site EUI of 88 kBtu/ft2/yr, which is 430 less than the median site property EUI of 518 kBtu/ft2/yr. The source EUI is designed to be 150, which is 736 less than the median source property EUI of 886 kBtu/ft2/yr. The median site property is a reference point that represents a typical building. Therefore, the McGoldrick Center far exceeds the energy efficiency of the typical building of its type.
Although the building consumes some natural gas through its heating system and other fossil fuels through the electricity it uses, these sources are offset partially by a large solar array on the roof and offsite renewable energy, as described in the next section.
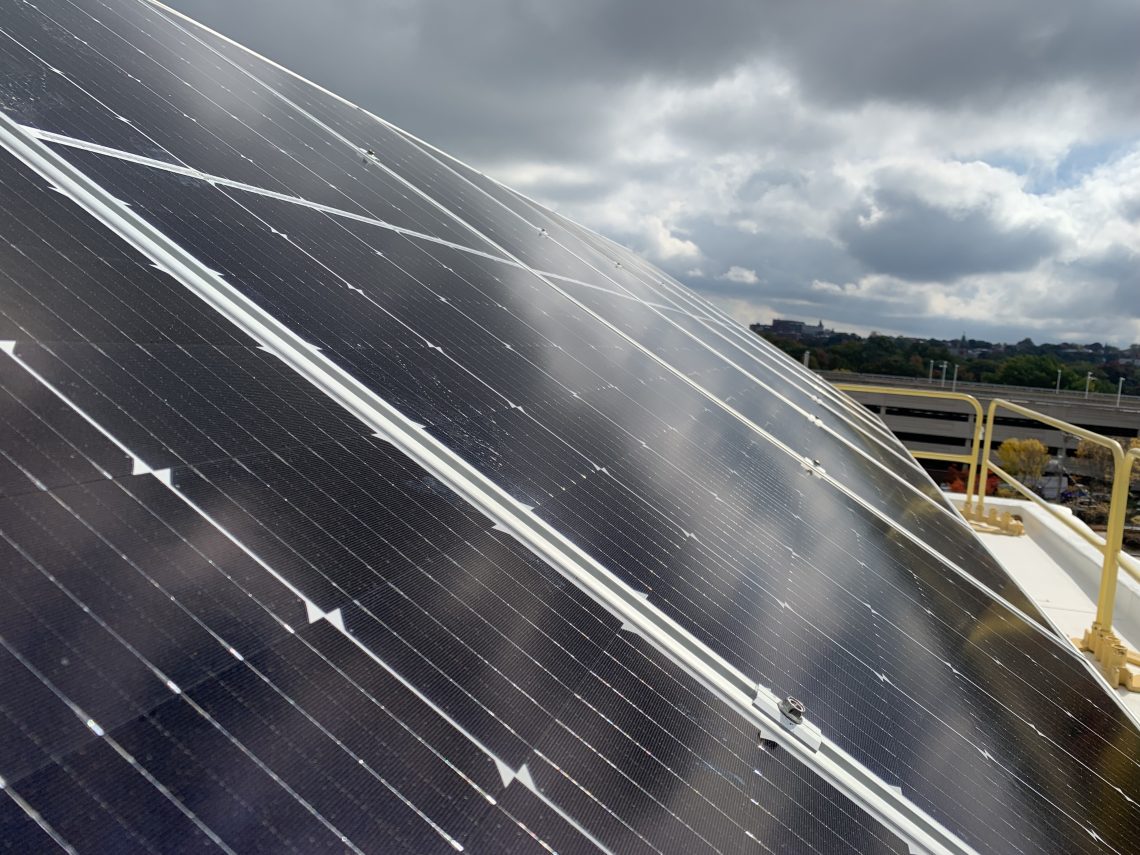
The roof of the McGoldrick Center features a large PV solar array. PV stands for photovoltaic, which is the type of solar technology that generates electricity, as opposed to other types, such as solar hot water panels. The size of the system is 30.2 KW DC and 33.3 KW AC. The panels are projected to produce approximately 37,680 kWhs annually, which is enough electricity to power the equivalent of 5.7 average Maine homes.
The system, installed by Revision Energy, consists of seven array blocks, each with a fixed tilt of 30 degrees and azimuth of 225 degrees. An estimated 7.11% of the building’s total energy load is offset by the solar array. The University retains all of the RECs associated with the project and does not sell them.
The McGoldrick Center’s electric load is being covered by renewable energy through a combination of the solar panels described under the Renewable Energy Onsite section of this site and the purchase of RECs (Renewable Energy Certificates) from renewable energy that is produced offsite. RECs are a claim on the production of renewable energy, as they represent a financial commitment to the production of that energy. One REC is equal to one megawatt hour (MWh). Solar, wind and other renewable energy produced offsite is still helping to mitigate carbon emissions, so long as only one entity is claiming that benefit through the purchase, retirement, or retainment of the RECs associated with it. Not only is the University being careful not to double-count RECs, but they are also ensuring that the RECs they purchase are Green-e certified. Green-e certification makes sure that the renewable energy is being created by new facilities that meet certain environmental impact, accuracy and transparency standards.
100% of the McGoldrick Center’s electric load will be covered by renewable energy for a period of five years at a minimum, starting at occupancy, and this commitment will likely continue well beyond that period. The renewable electricity offsetting the building is accounting for 66.3% of the building’s total carbon footprint, when you take heating into consideration as well.
Refrigerants are used in modern buildings in various heating and cooling applications. They are comprised of vapor gases or liquids that are used for transferring or expelling heat. You can find examples of refrigerants in refrigerators and freezers, as well as heat pumps. The environmental problem with refrigerants is twofold. First, some of them are especially potent greenhouse gases. Their relative impact on the greenhouse effect can be hundreds to even thousands of times higher than carbon dioxide on a per compound basis. Second, some refrigerants can deplete the ozone layer.
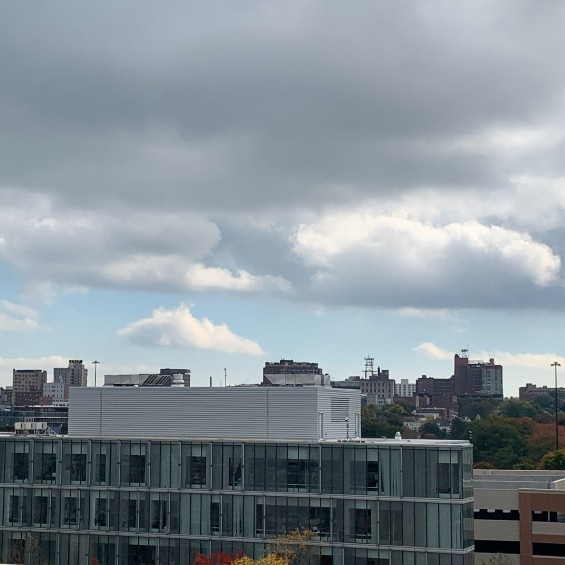
Many people don’t think about this issue anymore since the catastrophic effects of ozone depletion in the atmosphere were largely avoided by a multi-national effort in the late 1980s to limit the production of the type of refrigerants that cause the most egregious ozone depletion. This effort resulted in an agreement called the Montreal Protocol. Ozone depletion is harmful because it can result in an open layer in the atmosphere that allows too much radiation to hit earth’s surface, which can be harmful to life. Although the Montreal Protocol addressed ozone depleting compounds, it did not directly address the refrigerants that most acutely impact climate change, so responsible refrigerant management requires attention to both potential effects of the refrigerants that are chosen for use.
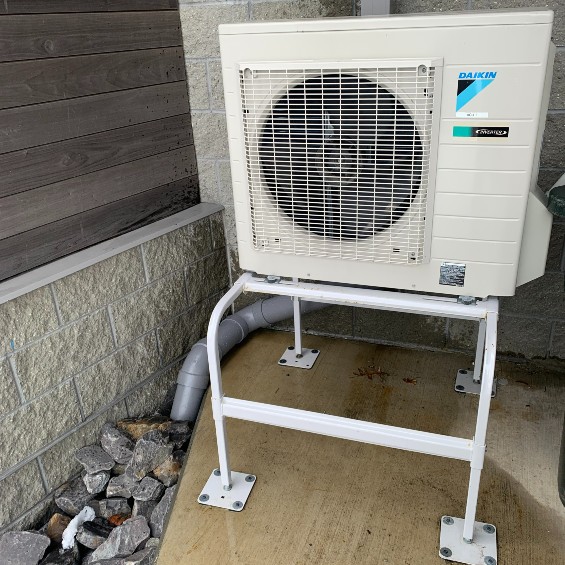
The equipment in the McGoldrick Center minimizes the emissions of compounds that contribute to both ozone depletion and climate change.
How well a building operates only represents part of its environmental footprint. Where a building’s materials come from, how they were extracted, how they were manufactured, and how far away they come from comprise the other half of the story.
The McGoldrick Center’s materials were carefully selected to meet as many sustainable criteria as feasible. The construction team prioritized the sourcing of material from manufacturers that publicly released reports, documenting information about their raw material supplies, such as extraction locations, commitment to long-term ecologically responsible land use, commitment to reducing environmental impacts from extraction and/or impacts from manufacturing processes, and a commitment to meeting applicable third-party standards of responsible sourcing.
Beyond sourcing from companies that are transparent about the impacts of their products, the McGoldrick Center construction team also tried to directly source as many materials as they could that meet at least one of LEED’s standards for responsible extraction criteria, such as bio-based materials, wood products, reused materials, materials with recycled content, and materials where the producer extends responsibility for the material beyond its usable life and into its “post-consumer” life.
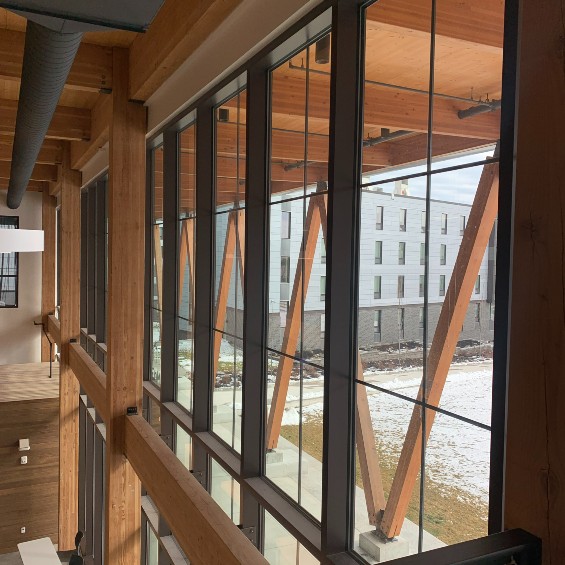
So, what are the numbers? The McGoldrick Center features 67 weighted products that meet LEED’s criteria for Environmental Product Declarations, 13.5 products that meet embodied carbon or life cycle optimization criteria, 58 products that meet material ingredient reporting requirements, and 5.5 products that meet material ingredient optimization requirements. A total of 35.7% of the raw materials used in the building were sourced sustainability.
The criteria and different categories can be confusing, so some examples may help. The McGoldrick Center features:
- CorianR Solid Surface, which comes with an environmental product declaration that explains its embodied carbon and embodied energy impacts
- EcoTouchR PinkR Fiberglass Batt & RoleTM insulation, which comes with an environmental product declaration that shows a flow chart of which raw materials were sourced, how they are shipped, etc.
- ThermafiberR Mineral Wool insulation, which comes with an environmental product declaration that lists all of the material inputs to the product and what their masses are, along with a flow chart of the manufacturing process
- Rockfon, which is a certified Cradle to CradleTM product at the silver level. The certification ensures products are healthy, circular in their recyclable value, meet clean air & climate protection goals, take care of water & soil, and promote social fairness, which includes human rights and fair labor practices.
- GreenScreen EvolveR, which is a certified Cradle to CradleTM product at the bronze level
- Modular Carpet, which comes with an environmental product declaration that provides the electricity and water consumption of the manufacturing process, along with the global warming potential of the embodied carbon in the material.
- Mass timber wood, including CLT and Glulam, which is a sustainable choice for structural support within the building
Mass timber is one of the most visible, and easy-to-conceptualize, sustainable materials used throughout the McGoldrick Center. Mass timber is a category that usually refers to pieces of wood that are glued together to create greater strength and span longer lengths than would be possible if they were by themselves. CLT (Cross Laminated Timber) is a form of mass timber that is used for horizontal applications throughout the building, such as decking.
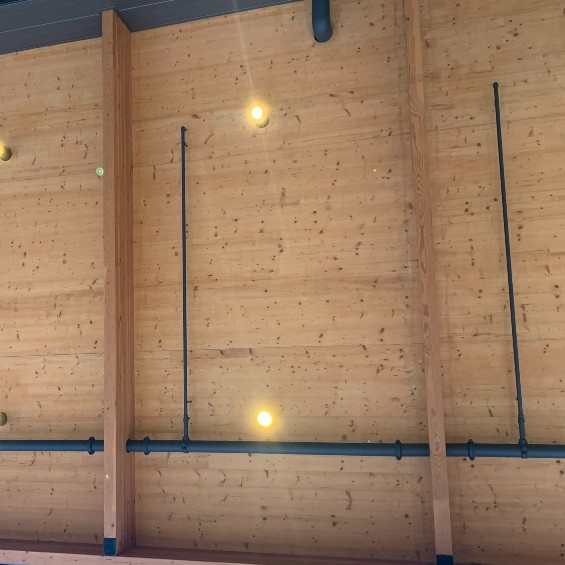
Glulam (Glue Laminated Timber) is a form of mass timber that is used for vertical applications throughout the building, such as support beams.
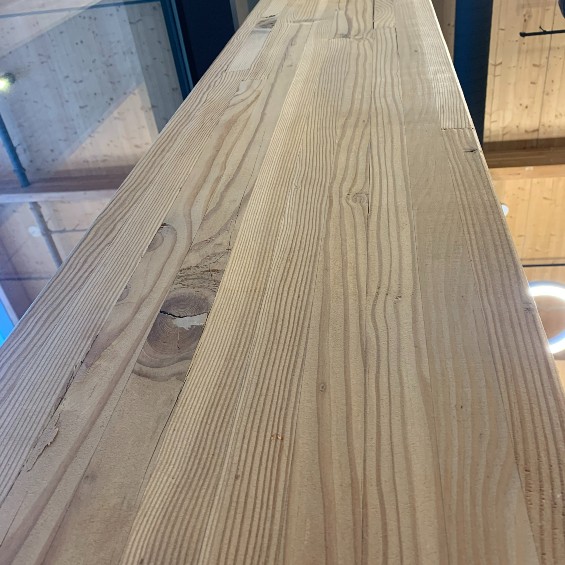
CLT and Glulam can be used in place of concrete or steel in many applications because it is especially strong. Since concrete and steel have such high embodied carbon and embodied energy, any minimization of their use is a reduction in the buildings’ environmental impact. Wood has far less embodied carbon or embodied energy because the raw material extraction process and manufacturing process use less fossil fuels. Wood is also a renewable resource, since new trees can be planted to replace trees that are cut down, as opposed to steel and concrete which are comprised of several ingredients that are now renewable.
Waste diversion in a LEED building starts before the building opens. The McGoldrick Center’s construction team worked hard to identify, sort, divert, and track as much waste as they could, including, but not limited to asphalt, concrete, cardboard, metal and co-mingled recyclable materials. Tracking efforts documented the weight of the material, the dates the materials were removed from the job site, and the receiving party. Their efforts paid off, as they were able to divert over 1,966 tons of waste. This amounted to a waste diversion rate of 93.96%, far exceeding their goal of 75%. Diverted waste was either recycled or salvaged.
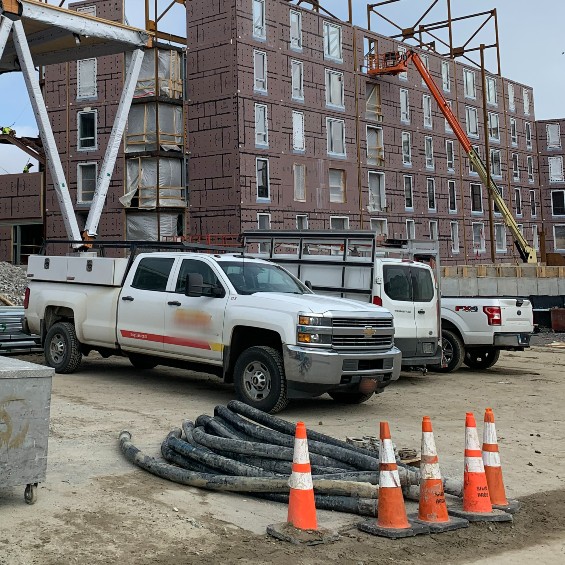
Food scraps and other organic matter is collected throughout the McGoldrick Center, so that it can be composted. Composting is an important way to divert waste from the landfill and preserve valuable nutrients that can serve another life in someone’s garden. Collection bins, like the one below, invite occupants to divert their food scraps. These bins are placed in locations where food is cooked, served and eaten. They are in both pre-consumer and post-consumer areas. Pre-consumer food scraps include things like vegetable ends, scrapings from pans and other items that are discarded in the cooking process. Post-consumer food scraps are bits of food that are left over after people are done eating.
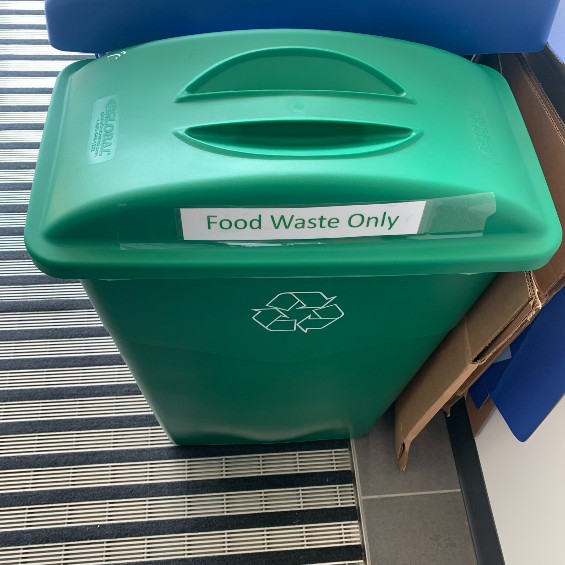
The University’s resource recovery department and dining services department periodically condense these food scrap collection bins into larger totes. The totes are stored in a dedicated, refrigerated storage closet designed specifically for food scrap collection. This closet is situated close to the loading dock in the back of the building, so that it can be easily accessed by a composting company, who comes 2-3 times per week to haul the scraps away.
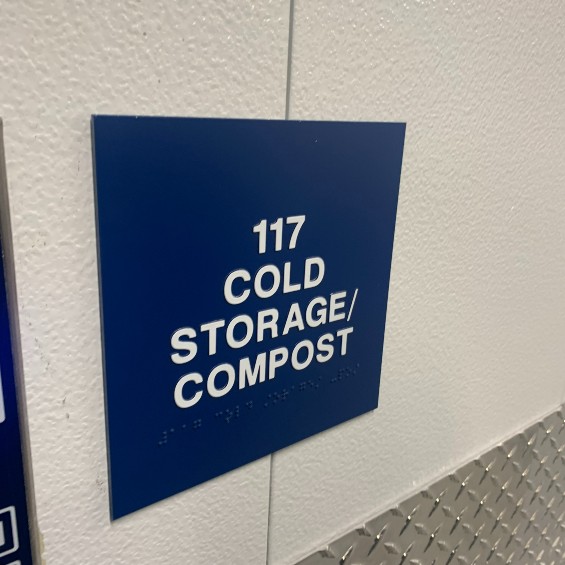
The company then processes the scraps into compost at a location off-campus. This nutrient rich compost is then used by local gardeners and farmers. Currently, the company the University is contracted with is Garbage to Garden.
Historically, the University has diverted over 100 tons of food scraps to compost annually.
The air quality within a building is important for the health of its occupants and visitors. The construction team for the McGoldrick Center used four main strategies for ensuring high indoor air quality.
First, they focused on acquiring building materials and furnishings that have less toxic chemicals and less off-gassing. Off-gassing is when a material releases gas or chemicals into the ambient air that can then be inhaled by people in the building. If you have ever noticed the smell of a new car, new carpet, or new t-shirt, you have experienced off-gassing.
LEED focuses on minimizing the off-gassing of VOCs (Volatile Organic Compounds). The McGoldrick Center construction team prioritized the purchase of low emitting supplies for paints & coatings, adhesives & sealants, flooring, ceilings, and insulation. 100% of the paints and coatings, flooring, ceilings and insulation were low-VOC. 100% of the adhesives & sealants met low VOC content evaluation standards, while 80% met low VOC emissions evaluation standards.
In addition to the buildings materials, special effort went into trying to acquire as many low-VOC furnishings for the building as possible by seeking furnishings that were BIFMA compliant, and in particular, furnishings that met ANSI/BIFMA’s emissions standards.
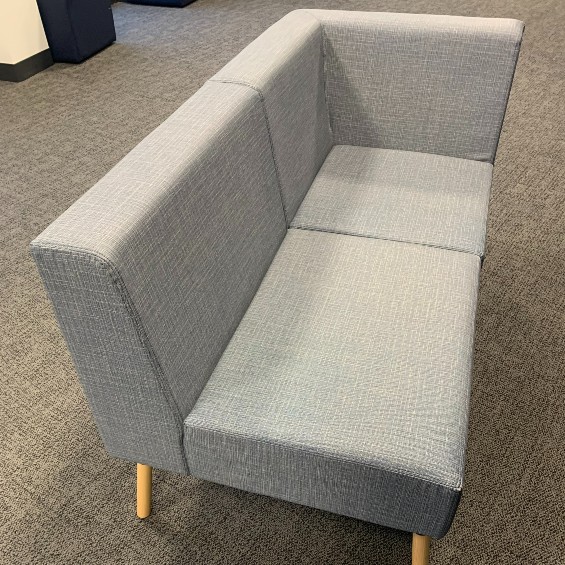
The second strategy was to ensure that building materials did not get dusty, damp, or moldy throughout the construction process. The construction team covered open ductwork with protective film, installed reinforced poly walls and temporary enclosures to retain heat and protect against moisture, operated pumps to remove any standing water that would occasionally collect, inspected all material before it entered the project site, received deliveries of material “just-in-time” instead of storing it on site where it was more vulnerable to damage or decay, and finally, wrapped unused materials in poly or secured them in clean rooms to prevent dust and water damage.
The third strategy was to mindfully design spaces that actively use or produce hazardous gases or chemicals so that there is sufficient separation of the air in those spaces from the building’s main air and that there is effective exhaust for those spaces. Additionally, the entire building was designed with adequate fresh air intake and exhaust of old air through its main mechanical systems.
The final strategy was flushing out the building to remove as much unhealthy air, particulates, and contaminates as possible before occupancy. Before the flush out began, all the MERV8 filters in the HVAC system were replaced, so that the flush out would be more thorough and effective. The total square footage of the building was multiplied by LEED’s requirement of 14,000 cubic feet of outdoor air per square foot of floor area to determine the total amount of air volume that the building would need to be adequately flushed. The team determined that a minimum of 15 days would be needed to cycle an adequate amount of air. They then began flushing at a rate of 27,050 CFM (cubic feet per minute) of outside air. All dampers were fully opened to allow for maximum air flow. During the process, the internal temperature of the building was maintained between 70 and 73.5 degrees to ensure the proper parameters required of LEED. The flush out duration lasted 39 days, far exceeding LEED’s minimum guidelines to acquire the points. After the flush out, the dampers were reset back to their designed position, and the MERV8 filters were replaced again so that the building could start with all clean systems.
The University of Southern Maine takes outdoor air quality just as seriously as its indoor air quality, and the design of the McGoldrick Center exemplifies this.
The University’s tobacco-free policy protects students, staff and faculty against unhealthy cigarette smoke. To remind people visiting the building that they can’t smoke, the University strategically posted several signs around McGoldrick in areas that could be attractive to would-be-smokers, such as the portico and the second floor balcony.
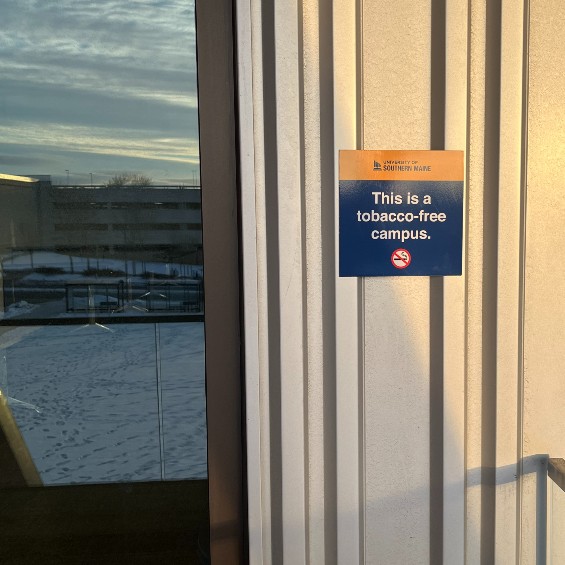
To further protect clean air on campus, the University has a no-idling policy, where vehicles are not allowed to leave their engines running when parked. This policy not only contributes to more breathable air on campus, but it also saves on unnecessary carbon emissions. In an effort to minimize the impact of tailpipe emissions on McGoldrick Center visitors from cars and trucks, the University purposely eliminated a large parking lot that would have engulfed the entire frontage of the building. In fact, the University did not place any parking near the building, with the exception of minimal parking for fleet vehicles and delivery drivers in the back of the building, by the loading dock. This loading dock is separated from pedestrians on the north side by a steep slope and on the south side by an enclosed walkway. These physical barriers not only keep pedestrians from entering the loading dock area, they also keep pedestrians a healthy distance from the fumes released in the loading dock area.
In addition to the human-made solar system on the roof of the building, the McGoldrick Center takes advantage of passive energy from the sun as well. Passive solar is the concept of absorbing energy directly from the sun without having to process it or transform it through a complex system. This energy can be utilized simply as heat, light, or both.
The portion of the first floor that borders the glass face of the building is comprised of a slab. This concrete can absorb heat directly from the sun in the colder months as it penetrates the building through the large glass panels. This free energy heats up the concrete and serves to help the building stay warm. Concrete can stay warm for many hours after being heated, so it can essentially act as a rudimentary battery, re-radiating warmth even after the sun goes down.
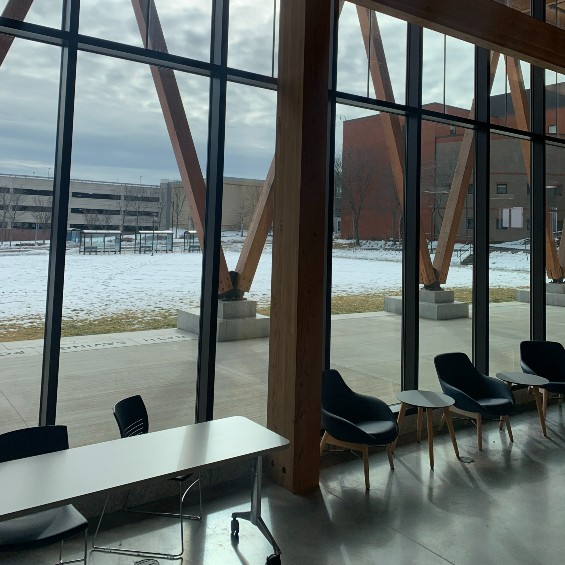
The McGoldrick Center also takes advantage of free light from the sun. This strategy, called daylighting, is maximized by the strategic placement of rooms, windows and infrastructure around the windows. For example, most of the large common rooms in the building are positioned on the eastern and southern sides of the structure, in order to capture daylight. Some of the windows have light shelves underneath them, which are metal shelves designed to bounce light deeper into a room, kind of like skipping a stone across the water.
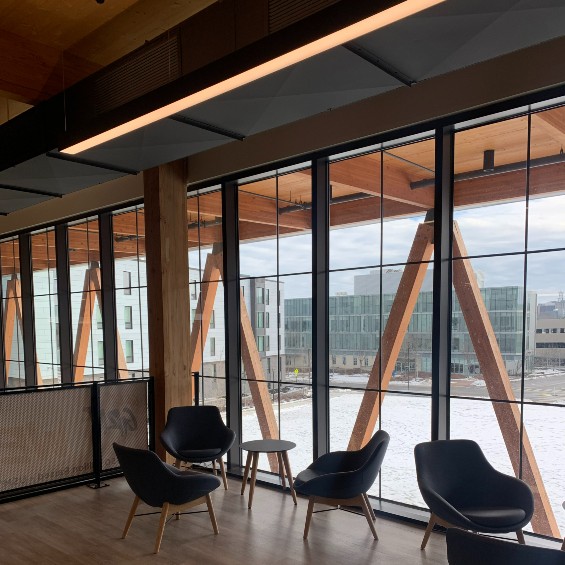
McGoldrick Center participates in demand response actions to support the University’s demand response goals. A demand response is when the University does its part to try to reduce electricity use during critical periods when the New England electric grid is close to maxing out its supply of electricity. These situations, which usually occur during hot weather events in the summer, pose challenges for everyone relying on electricity across the grid because they signal a potential brown out or black out, unless the grid can quickly fire up peak demand electric plants that aren’t normally adding electricity to the network. These plants are often heavy carbon producers as they often operate on fossil fuels, including oil or even coal. An alternative to firing up air-polluting plants is to have big electricity customers, like the University, work quickly to reduce their electric load on short notice. Not only does this have a positive impact on carbon emissions, but it also saves the University money since peak demand events are used by the utility company to help set the rates that the University will pay for electricity for the rest of the year. The less the University uses during the critical period, the less they will pay on their electric bill.
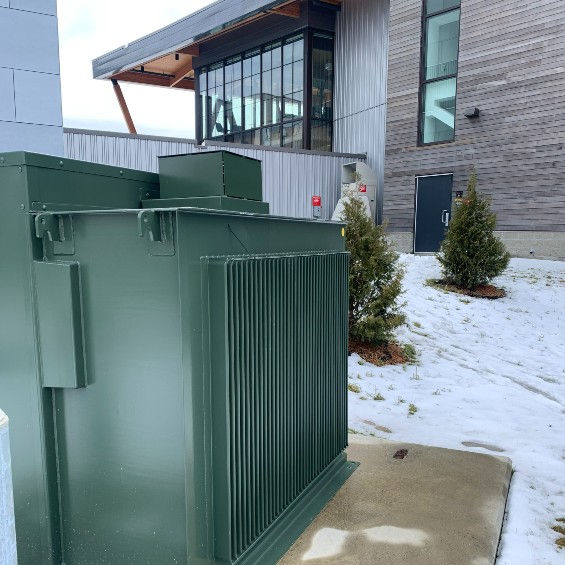
Prior to opening the McGoldrick Center, a team of experts from the University met with experts from the design and construction team to develop a plan for demand response. They figured out how they could reduce electric demand by at least 10% in the cooling and ventilation system if given just a couple of hours of notice. Although they did not pursue LEED points for this plan, it is still the University’s plan for reducing electricity in the building.
Green buildings are not just better for the environment. They are intended to be better for humans. The McGoldrick Center was designed to be comfortable for students, staff, faculty and visitors. Casual seating and study areas are placed throughout the building. Multiple types of seating options are available in the main dining hall, to allow occupants choices.

Thermal comfort is a major benefit of LEED buildings. An energy efficient building does not have to result in occupants being too hot or too cold. The thermal envelope around the McGoldrick Center is tight and well insulated, allowing the edges of the building to feel comfortable.
LEED awards points to buildings like McGoldrick for offering quality views, as well. The windows on the back side of the building look out on a small green bordered by mature trees that were strategically preserved as part of the project. The slightly raised green partially obscures the view to a small parking lot associated with another building, allowing viewers to see the quiet, residential neighborhood known as Oakdale.
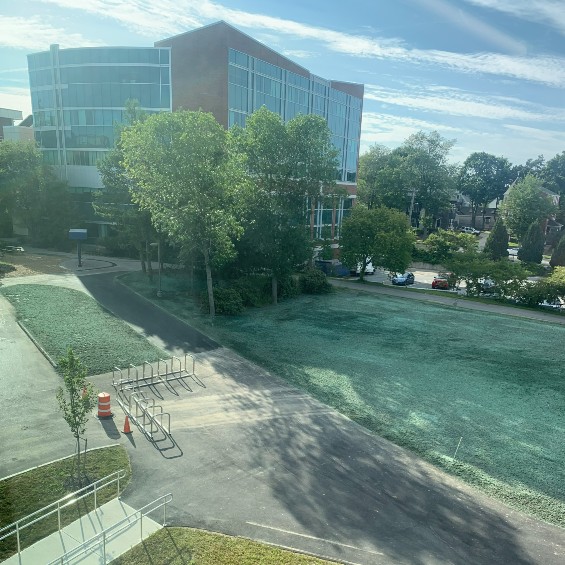
The first floor of the front of the building looks out on a large green from the slightly elevated vantage point of a spacious porch. The green is bordered by newly planted trees. This new green replaces what used to be a large surface parking lot. The decision to create this green transformed the center of campus from a monument to car culture to a comfortable outdoor gathering space where people can play frisbee, study, and build community. This new quod is not only a welcomed place for nature, but it is also surrounded by other green buildings, such as the new Passive House residence hall Portland Commons, and two other LEED Gold buildings: Wishcamper & Abromson. From the second and third floors of the building, occupants can look past the green to the beautiful, downtown skyline of the City of Portland, Maine’s largest city.
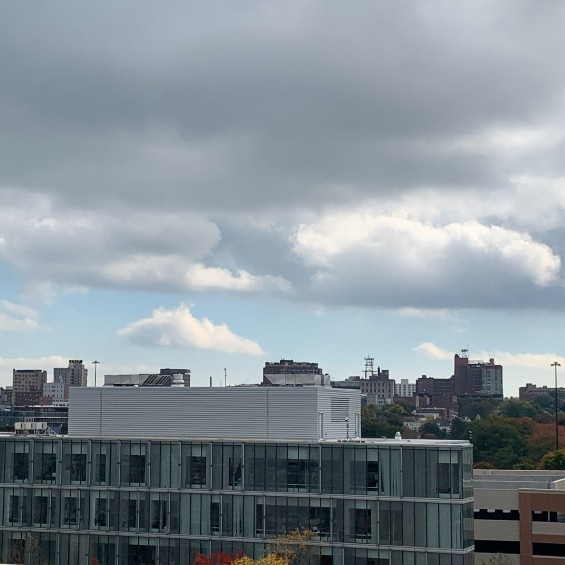